Breaking Free from
"We've Always Done It This Way"
You've delivered on deadlines, navigated labor shortages, and weathered material cost fluctuations. Your reputation is built on solving tough problems with proven methods. But what if those familiar methods have become your biggest liability?
Traditional building systems—particularly pre-fabricated metal buildings—have long been the industry default. But today's challenges—impossible schedules, stringent sustainability requirements, unpredictable weather patterns, and soaring client expectations—are exposing the limitations of conventional construction approaches.
This guide isn't about abandoning what works. It's about expanding your toolkit with hybrid structures that combine robust steel frames with high-performance cladding and insulation options, giving you a strategic alternative when specific projects demand speed, flexibility, or exceptional resilience.
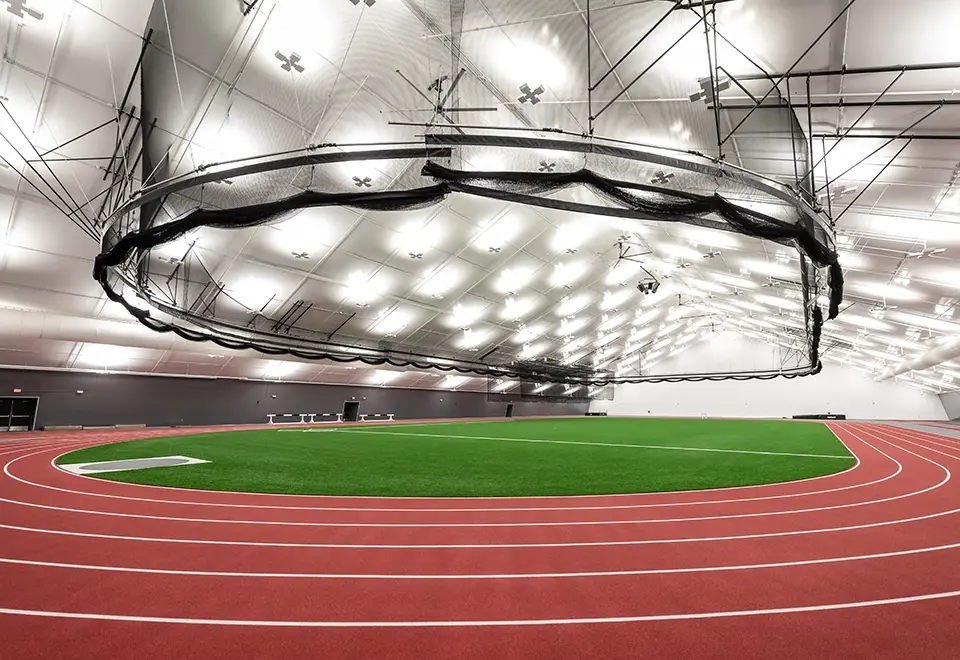
Is "We've Always Done It This Way" Costing You Jobs?
Learn how innovative contractors can win bids, beat deadlines, and solve today's toughest construction challenges.
Demanding Expectations
Your clients aren’t just comparing your bid to the one next door. Their expectations are shaped by every frictionless, fast, and personalized experience they’ve had in other industries. You’re no longer just a builder. You’re expected to be a problem-solver, an advisor, and a strategist.
Are your current tools enough?
Sustainability Mandates and Energy Efficiency Requirements
Sustainability used to be a buzzword. Now it’s written into code, contracts, and corporate strategy.
Your clients care about it, because their bottom line depends on it:
- Distribution facilities face energy costs that have doubled or tripled.
- Municipalities require net-zero-ready performance.
- Fortune 500 clients with board-mandated emissions reduction targets.
Traditional structures often require expensive additions to meet these standards. Fabric buildings reduce thermal bridging and maximize natural daylighting, delivering superior energy efficiency at a lower cost. At Legacy, we can provide traditional facade options, but we also offer a unique fabric cladding alternative (either exterior, interior, or both) that reduces thermal bridging, minimizes air-infiltration, and/or maximizes natural daylighting, delivering superior energy efficiency at a lower cost.
Many Legacy Building Solutions clients report 15-25% lower energy consumption than conventional metal buildings.
It’s about building smarter, leaner, and with lower operating costs—for you and your clients.
Why "We've Always Done It This Way" is Becoming a Liability
Familiar methods are comfortable. But they can also hold you back, especially when:
- Weather delays stretch your schedule and your client’s patience.
- Labor shortages leave you short-staffed.
- Material price volatility threatens your margin mid-project.
These problems aren’t going away. Hybrid construction gives you a new way to solve them—through shorter timelines, lighter foundations, and off-site fabrication that reduces weather risk and on-site labor needs.
You don’t need to ditch conventional methods. But clinging to them exclusively limits your ability to adapt.
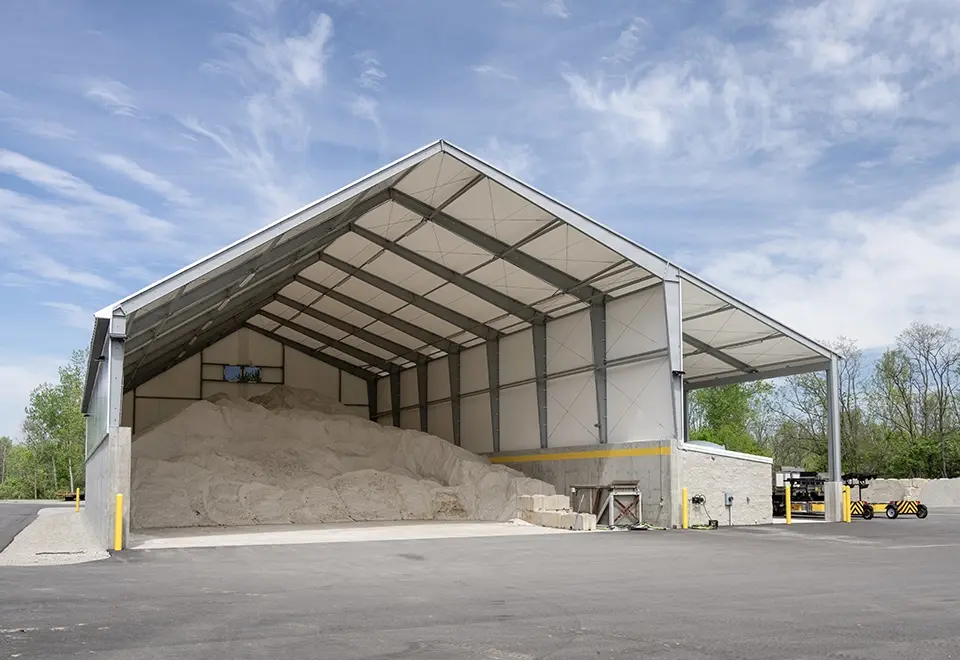
Hybrid Building Requirements vs. Traditional Solutions
Lifecycle Cost vs. Initial Price Tag
Your client asks, “Why is this more expensive upfront?” But you know the better question is, “What will this cost over 30 years?”
For certain environments, traditional buildings rack up higher costs over time. It’s driven by corrosion from fertilizer, salt, or humidity, roof leaks and energy loss, and maintenance that your client isn’t staffed to handle.
Hybrid buildings offer long-term value through corrosion-resistant materials, lower maintenance needs, and superior thermal performance.
It’s not about upselling—it’s about protecting your client’s investment. When you frame the conversation around lifecycle value, you shift from contractor to advisor.
Construction Timelines That Meet Market Realities
You've had the uncomfortable conversation before: explaining why a building needed to meet an urgent business need will take twice as long to construct as the client hoped.
Juggling deadlines is constant pressure. Over-promise, and clients are angry. Under-promise, and you lose out. Traditional is step-by-step: design, permits, then the domino effect. One delay can wreck the whole schedule.
Your clients are done hearing excuses. They're watching opportunity costs pile up every week they’re not operational.
Hybrid construction helps you avoid major timeline killers:
- Parallel workflows: Foundations are poured while the structure is built off-site.
- Reduced on-site time: Components are pre-manufactured and installed quickly.
- Fewer weather delays: Less work exposed to unpredictable elements.
This is a smarter sequencing strategy that compresses your schedule without sacrificing quality and puts clients in their buildings faster.
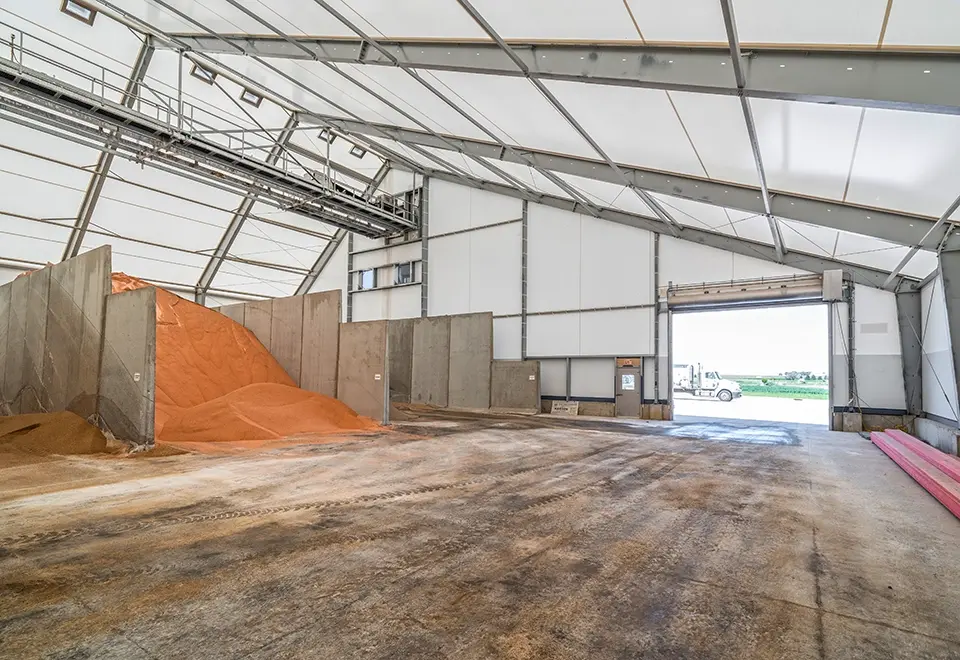
Critical Decision Points
Building for Adaptability
Every job site has its quirks: unstable soils, tight access, harsh climates. The solution isn’t always to muscle through it with the same old, hot-dipped galvanized or polyethylene approach.
Hybrid buildings offer site-specific advantages, like lighter structural loads, corrosion-resistant coatings on steel frames, durable fabric, and flexible connections. This means simpler, cheaper foundations on poor soil, longer life in coastal or caustic environments, and better performance in seismic zones.
Instead of forcing a traditional build where it doesn’t fit, hybrid systems can help you engineer around the obstacle and keep the project on track.
Smart Material Choices
Every project needs the right materials, not just the familiar ones. An airplane hangar isn't a fertilizer plant; a beachfront warehouse isn't a storage shed.
Material selection directly impacts energy efficiency, maintenance requirements, and building lifespan (extending useful life in harsh environments).
The optimal material isn't about tradition—it's about performance. By recommending materials precisely matched to your client's operational needs, you deliver measurable value they'll appreciate for decades.
Managing Labor Challenges
The skilled labor shortage is a persistent challenge. Relying on traditional builds and generalized subcontractors can mean scheduling headaches and quality risks you can't afford.
Hybrid building flips the script. More factory-built components mean less reliance on jam-packed job sites. Specialized crews, provided by vendors like Legacy with experience in fabric construction, get the job done faster, shrinking your labor hours and slashing schedule risks.
Hybrid shifts the labor equation. Less general on-site work, more efficient, specialized teams. Bottom line: Explore building methods and partners that ease the construction burden—it's essential for staying on schedule and in control.
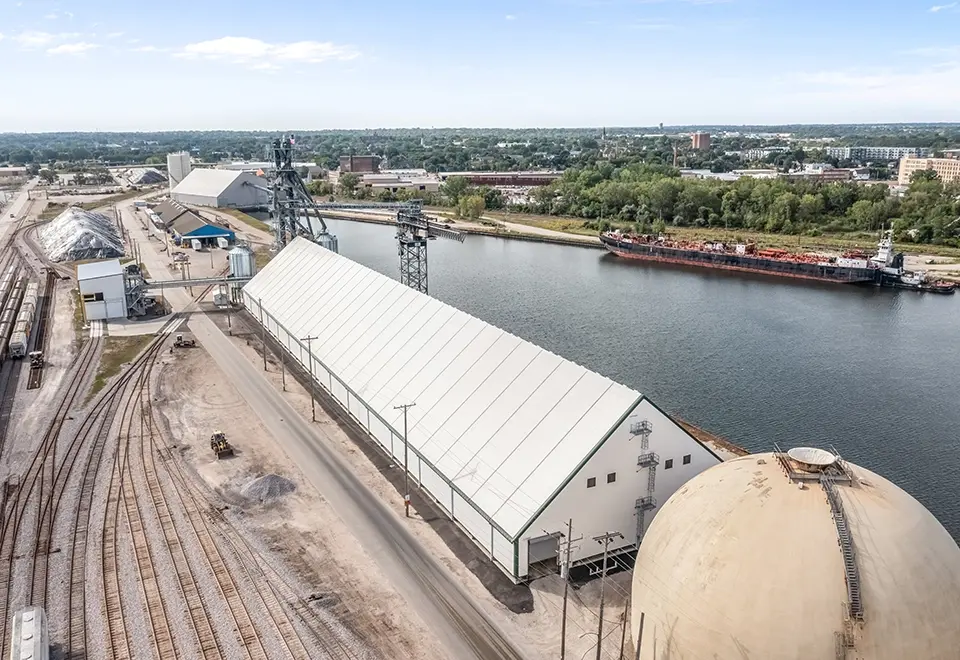
Smart Materials, Smarter Builds
Smart choices lead to smarter builds. It's about understanding that different projects demand different strengths.
Hybrid structures can achieve clear spans up to 300 feet, offering greater layout flexibility than traditional builds, which become expensive beyond 100 feet.
In energy-sensitive projects, fabric structures can outperform metal in blocking heat transfer, leading to significant long-term savings. In corrosive environments, fabric offers superior resistance, minimizing maintenance and extending lifespan.
- Legacy’s high-tensile ExxoTecTM PVC fabric offers long-term resiliency against heavy snow loads, hurricanes, derecho winds, and other extreme weather conditions. If the ExxoTec™ ever becomes damaged or worn, repairs are fast because the membrane is designed and installed as individual panels.
Your clients aren't just buying a building; they're investing in decades of reliable performance and value. That's why safety, durability, and long-term costs are critical considerations.
Hybrid buildings are engineered to meet the same rigorous standards as traditional construction (IBC, ASCE 7, etc.).
- Specialized hybrid and fabric suppliers go even further with compliance. Legacy prides itself on ISO 9001 and CSA A660 certification every year. We’ve also achieved Florida Product Approval, as well as other certifications including CWB, CAL FIRE, and AWS.
Steel frames are fully engineered and certified, while fabric envelopes are designed to withstand wind, snow, seismic loads, and fire, with robust connection details ensuring structural integrity.
Hybrid structures also prioritize longevity. Steel frames feature advanced coatings for enhanced corrosion resistance, and fabric is UV-resistant with warranties of 15-25 years and even longer real-world lifespans. This durability translates to long-term value.
With a hybrid envelope, the reduced energy consumption and lower maintenance translate to significant savings and a faster return on investment. By focusing on lifecycle costs, you can demonstrate the true value of hybrid solutions and build lasting client relationships.
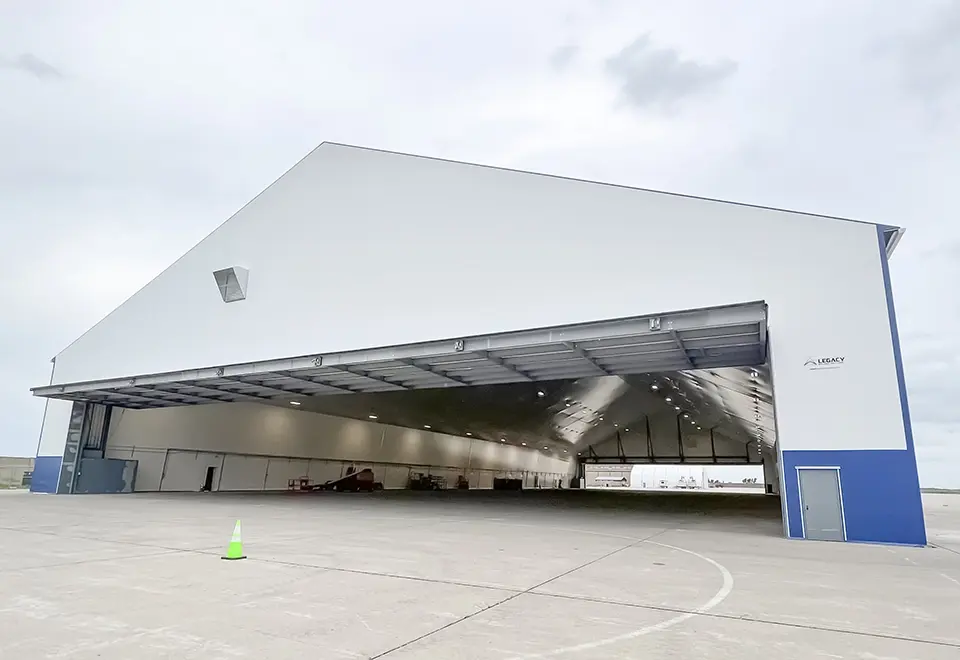
Project Planning
Smart contractors plan meticulously, especially when using new approaches. Hybrid methods allow you to bring suppliers in early. Their expertise avoids headaches with site plans, MEP, and operations, catching problems before they cost you.
- Permitting can be different. Hybrid structures are code-compliant, but officials might not be as familiar. Early communication and solid documentation are your best defense against delays.
- Scheduling shifts with hybrid. Parallel manufacturing changes the critical path. Know those factory lead times to maximize speed advantages.
- Performance specs are crucial. Don't just meet minimums; define exact needs for temperature, loads, and expansion. Get the right system, not just one that works.
- Solid pre-planning cuts risk, period. It means recommendations based on facts, not assumptions, and builds that go smoothly because everyone's on the same page.
Allocating Resources Effectively
Different builds mean different resource needs. Hybrid often means more design upfront, which means changes after manufacturing starts can hurt. Plan that design phase carefully—or seek assistance from a supplier that can do it all for you.
Hybrid can also shift labor needs. Juggling subs is a constant challenge. More trades, more headaches with schedules and quality. Hybrid can simplify this. Equipment needs change, too. You might need less heavy equipment on-site, for shorter periods. That’s good for tight sites and your bottom line.
Often, the main supplier handles design, manufacturing, and installation, which means fewer cooks in the kitchen and clearer accountability. System integration gets easier, too. MEP connects to standardized elements, resulting in less field guesswork and fewer problems down the line. Less on-site work with hybrid means less trade stacking, fewer scheduling nightmares, and a safer site.
You're still the conductor, but with fewer instruments to manage, and more time ensuring the system delivers for your client.
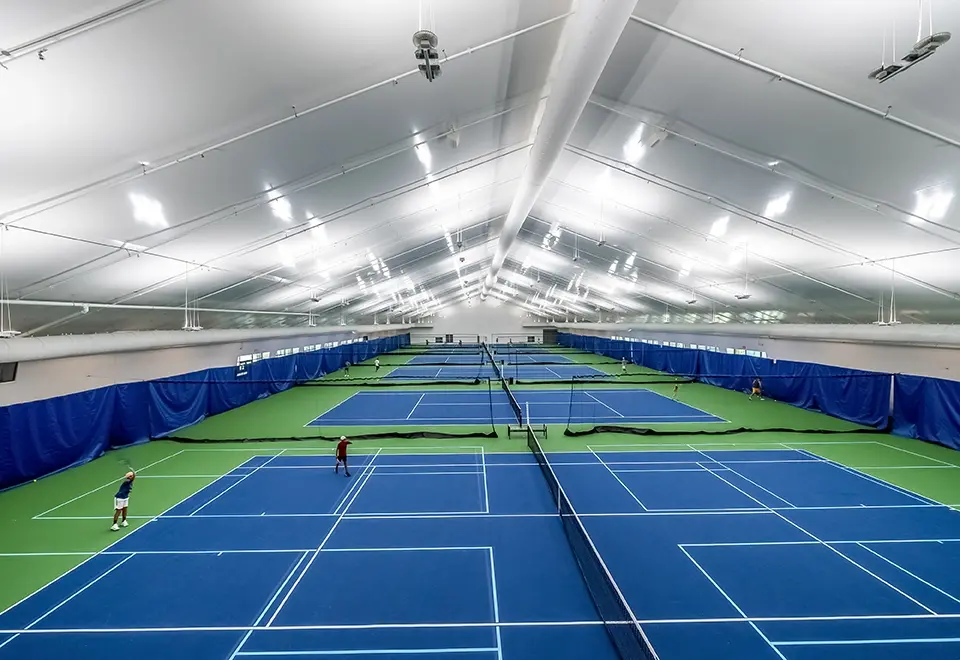
Expert Consultation
It's not about one system being best, but about the right system for the right job. Your value is in helping clients navigate these choices.
Legacy Building Solutions provides comprehensive support for contractors exploring hybrid structures, including:
- Project-specific assessment: Detailed evaluation of your specific project requirements and considerations to determine whether a hybrid approach offers advantages over traditional construction.
- Comparative analysis: Side-by-side examination of hybrid vs. traditional approaches for your application, with transparent discussion of the advantages and limitations of each.
- Integration guidance: Expert recommendations on incorporating hybrid structures with other project elements to create cohesive, high-performing facilities.
- Client education: Resources to help your clients understand building system options and advantages, supporting your role as their trusted construction advisor.
By partnering with specialized experts, you can confidently evaluate innovative building approaches without developing comprehensive in-house expertise. This collaboration strengthens your position as a trusted advisor while expanding your ability to solve increasingly complex construction challenges.